Utilization of Metal 3D Printing in Aerospace
- Himgiri 3D
- Dec 12, 2018
- 4 min read
Updated: Aug 13, 2019
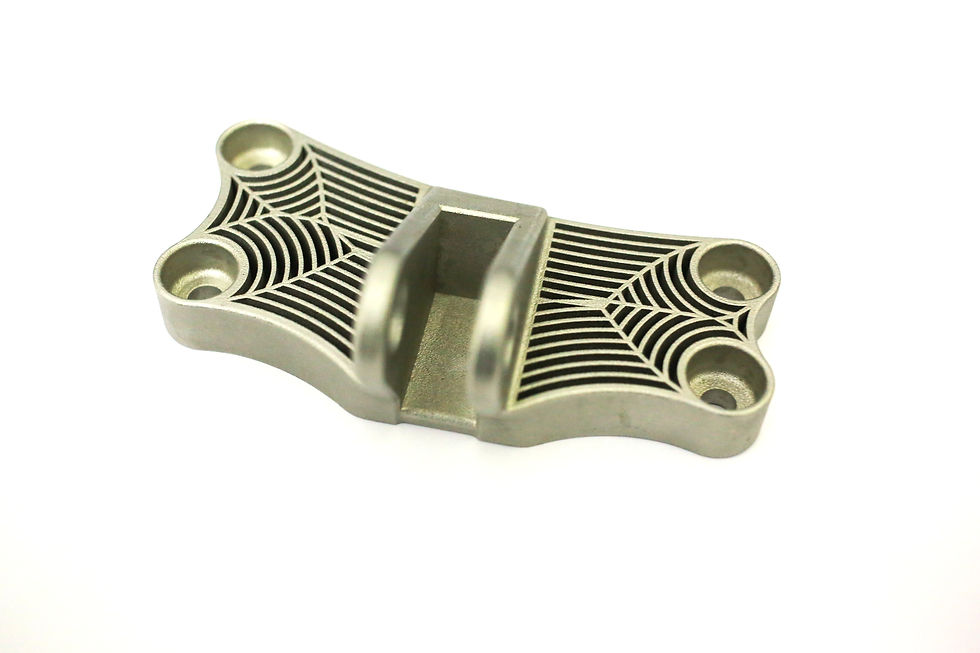
Metal Additive Manufacturing offers unmatched flexibility in terms of part geometry, material composition and lead time. It is moving towards revolutionizing the aerospace manufacturing sector through production of highly complex, lightweight parts with reduced material waste. It can also be employed for repair of complex components such as engine blades/vanes, combustion chamber, etc. Complex geometry thin walled aircraft engine components and structures, difficulty in machining of materials are other main factors forcing aerospace sector to adopt the use of additive manufacturing technology.
Currently machining, forging and other conventional processes are producing the aerospace parts. There is an extreme waste of highly expensive material in the conventional manufacturing processes and only less than 5 % of the original material is the content in the finished part. In case of Additive Manufacturing there is maximum utilization of material and also produces near net shape parts.
GE Aviation has been evaluating Additive Manufacturing for over a decade and now it has successfully produced Leap Engine Fuel Nozzle in cobalt chrome by laser AM melting process. The Leap engine fuel nozzle has already cleared ground-based engine testing and has been certified for use on civil aircraft. The AM part has replaced an assembly of 20 components with reduced cost, weight, without joints and improved performance.
SAFRAN Group is another organization that has identified additive manufacturing process as a breakthrough technology for a number of engine components for development of prototype and engine both Turbomeca and Snecma. Turbomeca, which makes helicopter engines and Snecma aircraft engines, extensively used this technology in the design phase. Snecma has guide vanes for the silver-crest business jet engineand manifold for Vinci rocket engines, hydrogen turbo pump. Snecma has successfully used the technology for speedy implementation of design changes and also for repair of components. Extensive researches have been under taken to develop complex assemblies as integrated single component by this process. Examples are guide vane assemblies, integrated fuel manifold and combustion chamber.
NASA engineers used Additive Manufacturing technology to produce intricate metal rocket injector part for their next generation Space Launch System (SLS) J-2X engine.Rocket injector was manufactured from selective laser melting (SLM) additive manufacturing process using nickel–chromium alloy powder. The traditionally manufactured injector had 115 parts and 3D printed injector had only two parts. Additive Manufacturing process considerably reduced the manufacturing time needed to produce injector part from months to weeks. The part was built into single piece without joints, which was structurally stronger and more reliable leading to the overall safety of the vehicle. It was a significant improvement in saving time and cost for NASA. This part will undergo structural and hot-fire tests and finally will be used in the J-2X engine.
The leading commercial aircraft manufacturer Airbus has been increasingly gaining the importance of Laser Melting of Metal Powders in aircraft manufacturing. The Cabin bracket connector used in the Airbus A350 XWB was additively manufactured using Laser Melting technology. Earlier this part was milled and machined out of aluminium alloy and now it is a 3D printed part, which is made out of titanium (Ti) powder material with a more than 30 % weight reduction. Milling of aircraft parts leads 95 % waste, which can be recycled whereas with additive manufacturing the percentage of waste is only 5 %. In AM process tools are not required to produce functional sample part thereby eliminating the tool cost. This also helps in identifying early stage design errors and design optimization. Earlier Airbus projected 6 months to develop component and now it has reduced to 1 month.
Additive manufacturing technology helps aerospace manufacturers reduce costly design challenges, and downtime, whilst innovating faster, testing more thoroughly, and producing customized, flight-ready parts. The aerospace industry is constantly pushing technological boundaries to reduce weight and increase vehicle performance. Additive manufacturing accomplishes those goals.
The advancement of 3D printing materials offers terrific weight savings in comparison to traditional manufactured parts and enables economical production of incredibly complex shapes that are often found in aerospace vehicles. It’s therefore not surprising that the industry is increasingly looking to the technology to realize those gains. AM completely redefines the economics around a make/buy decision. Instead of making one decision during the development phase about producing or buying a certain part, access to additive manufacturing technology enables you to make that call at every procurement.
Based on your current capacity and the urgency for the part, you can choose to produce it within your own facility, or outsource it to a qualified supplier. The ability to produce the same part on another qualified machine allows you to move around production for better efficiency and risk reduction. AM also has great environmental benefits. First and foremost, it’s the fuel reduction achieved from light-weighting of parts.
Additive manufacturing helps reduce weight in two ways. First, since the part is built up, rather than cut out of a solid block, the opportunity exists to tailor the geometry so that only the material needed to carry the load is used. This saves on waste material and reduces the buy-to-fly ratio. This can also make for some very complex yet elegant skeleton-like parts and also applies to internal geometry. You can’t machine the inside out of a closed part, but some additive manufacturing technologies enable the production of a very sparse interior, which can result in large parts that are very light.
However, process repeat-ability is the key and any equipment or process for use in a production environment will need to demonstrate this repeat-ability and Additive Manufacturing has earned a respectable position in this criteria. With further advancements, more and more aerospace equipment parts and components will be manufactured using AM and the benefits of the same will be known to the industry.
Comments